Planlanamaz olanı planlamaya çalışmak. Günümüz müşterileri, daha fazla seçenek, daha fazla ürün ve daha kısa zamanda teslim süreleri talep eden üreticilere meydan okuyor. Ürün Ağacının artan karmaşıklığı ile doğru zamanda doğru stoka sahip olma görevi daha da zorlaşıyor.
MRP ile planlamanın ilk günleri
Andrew Burton ,40 yılı aşkın sürede Üretim ve Tedarik zincirinde çalıştığı süre boyunca, stok kartlarının yerini alan bilgisayar sistemlerinin ve ‘Denge Çizgileri’ çizelgelerinin tanıtımını görmüştür. Tamamen manuel sistemden otomasyon düzeyine geçilen büyük bir kademe değişikliğidir. Bir sonraki adım 1960’larda MRP (Malzeme İhtiyaç Planlaması) idi. Bu yeni süreç, doğru bir Ürün Ağacına ve doğru stok kayıtlarına dayanıyordu. Bu, Üretim Planlayıcılarına en üst düzey üretim planını karşılayacak parçaları sipariş etme şansı verdi.
Önümüzdeki birkaç yıl içinde sistemler geliştikçe, diğer süreçlerin entegrasyonu da gelişti. Talep ve stok pozisyonundan satın alma siparişleri oluşturulabilir. Bir sonraki büyük adım, üretim kapasitesini getirmekti ve MRP II (Üretim Kaynakları Planlaması) oluşturuldu. Bu yeni özellikler 1970’lerde yayılmaya başladı.
MRP ve MRP II’nin temelleri hala basit bir Ürün Ağacında bulunuyordu. Her iki yöntem de sıfıra ulaşan bir plan oluşturmaya çalışır. MRP ve MRP II itme sistemlerdir, sipariş edilenin/planlananın sistemin ihtiyaç duyduğu zaman aralığında yapılacağını varsayarlar.
MRP, ERP’ye dönüşüyor
Önümüzdeki birkaç yıl içinde MRP sistemleri, daha hayati iş süreçleri getiren ERP sistemleri (Kurumsal Kaynak Planlaması) haline geldi. CRP (Kapasite İhtiyaç Planlaması), üretim ortamında olup bitenlerden bir geri bildirim getirmek ve bir çekme sisteminin bir unsurunu tanıtmak için ERP’nin bir parçası oldu. Bin yıllık dönem yaklaştıkça, üretim bu ERP sistemlerine daha fazla bağımlı hale geldi. Müşteriler daha fazla çeşitlilik ve özelleştirme talep ettikçe üretilen ürünler daha karmaşık hale geldi. Müşteriler, gerekli olan uzun teslim sürelerini beklemeye hazır değildi. Müşterinin neye ihtiyacı olabileceğini tahmin etmek giderek daha zor hale geliyor. Değişken bir tedarik zinciri ekleyin ve zorluklar, her ihtimale karşı tahminde bulunma veya stok bulundurma noktasına kadar birleştirilir! Ekstra envanter, kıtlığı önler, ancak yalnızca bir kısmını. Hala eksiklikler olabilir. Ekstra envanter, nakit ve depo alanını birbirine bağlar. Ekstra envanterin raf ömrü varsa, kullanımdan önce süresinin dolma ve israfa yol açma riski vardır.
Tedarik, yapı veya müşteri talebi varyasyonları nedeniyle bir üretim planı değiştiğinde, MRP çok sayıda kuraldışı durum iletisi üretecek ve birçok parçanın vadesi aynı tarihte olan ve çoğu gecikmiş olan talepler olacaktır. Bu mesajları en acil olanlara göre sıralamak mümkün değildir, bu nedenle önce harekete geçecek olanları belirleyemezsiniz.
Bu tedarik sorunlarına olası bir çözüm 2016 yılına kadar geliştirilemedi. Bu, DDMRP’nin üretim için ileriye dönük bir yol olarak ilk önerildiği zamandır. Yalın üretim düşüncesini ve kısıtlamalar teorisini aldı ve tahminin zor olduğu arz ve talebe bakmanın farklı bir yolunu buldu.
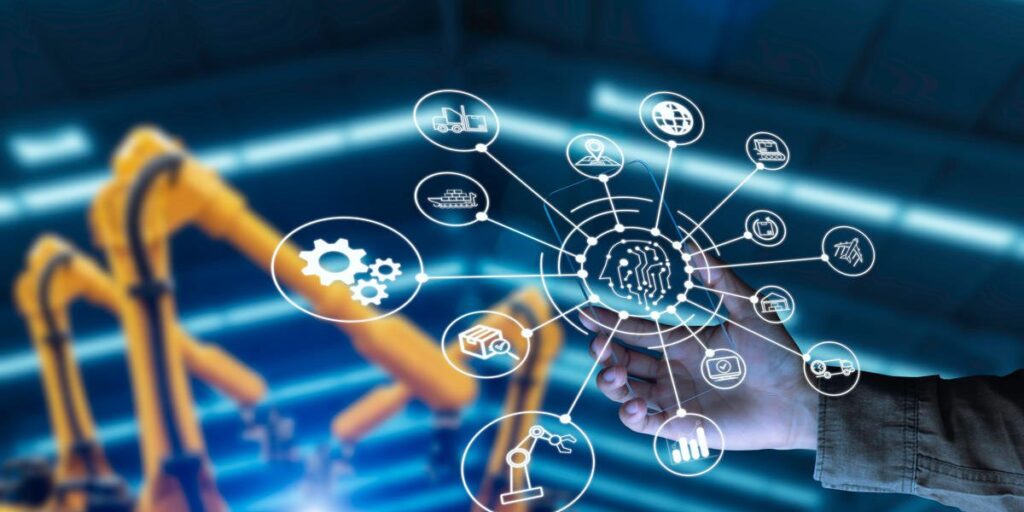
Cevap DDMRP mi?
DDMRP (Talep Odaklı MRP), geleneksel MRP’nin işlevselliğini geliştiren malzeme kontrolü ve yenileme yaklaşımı olarak tanımlanmaktadır. DDMRP talep odaklı olduğundan, üretim tesislerinde kıtlığa, üretim kesintilerine ve kaosa neden olabilecek talep ve arzdaki değişikliklere karşı daha hassas ve duyarlıdır.
DDMRP, MRP’nin bir uzantısıdır, ikame değildir ve planlanması gereken tüm parçalar için uygun değildir. Bir parçanın olası talebi karşılayacak yeterli stoka sahip olup olmadığını belirlemek için güncel kullanıma ve ileriye dönük tahmine bakarak çalışır.
DDMRP güncel tüketimi kullandığından, bir ürünün toplam tedarik süresini azaltmak mümkündür, böylece yenileme MRP’nin normalde önerdiğinden daha erken gerçekleşebilir.
Yakın tarihli bir IFS Teknik Raporu, DDMRP ve Yalın Üretim, tam da bu noktadan bahsediyor. “Bir planlayıcının belirli bir talebi karşılamak için yeterli parçaya sahip olup olmadığını belirlemeye çalışacağı geleneksel ürün ağacı odaklı planlama ve çizelgeleme yerine, DDMRP kapsamında envanter seviyelerine bakacak ve eldeki mevcut envantere hangi talep düzeyini yanıtlayabileceklerini belirleyecekler. DDMRP ayrıca sevkiyatın önündeki stratejik yerlere, darboğazlara veya değer akışının işletme için anlamlı olan diğer kısımlarına tamponlar ekler”.
DDMRP’nin yapılandırılmış bir metodolojisi vardır: Konumlandırın – Koruyun – Çekin:
- Konum: Ürün ağacı, yapılar içindeki kritik noktalarda stratejik öğeleri (malzemeler veya bileşenler) belirlemek için incelenir. “Kısıtlar” olarak bilinen kritik kaynakların üretim sınırlamalarını belirlediği Kısıtlar Teorisi yönteminin bir uyarlamasında, bu kilit materyaller diğer tüm bileşenlerin üzerinde kontrolün odak noktası olmalıdır.
- Korumak: Bu kritik öğelerin mevcudiyeti, envanterin tampon olarak kullanılmasıyla da sağlanır. Ancak bu tampon stok, ilk MRP planlama formülünün bir parçası olarak dağıtılmaz; bunun yerine, gerektiğinde dinamik olarak yenilenir.
- Çekmek: Tampon envanteri, envanter seviyelerini sürekli olarak izleyen ve arabelleği belirli bir aralıkta tutmak için görsel ipuçlarını kullanan yenilikçi bir çekme tekniği ile yönetilir.
DDMRP, mükemmellik için değil, insanlar için üretilmiştir. Bir tahminde bulunmak her zaman zor olmuştur ve çok azımız bunu doğru anlıyoruz. DDMRP tüm endüstrilere uygun değildir, ancak değişen malzeme taleplerinin sürekli takibini ortadan kaldırarak bazı parçalarda çok etkili bir şekilde kullanılabilir.
Andrew Burton’ın görüşüne göre, DDMRP, sürekli değişen tahminler ve müşteri özelleştirmesi ortamında yardımcı olmak için üretime başka bir araç sunmaktadır.
Kaynak: Andrew Burton
IFS Industry Director – Manufacturing
Tarih: 4 November 2021